High-tech industries such as the semiconductor industry require very precise and high quality tube preparation and welding. Tubes are usually welded using TIG, manual or orbital welding. Proper preparation is essential for any TIG welding operation to achieve a burr-free surface and perfect perpendicularity squareness.
Tubes with thin walls and small diameters require special attention as a deformation of the tube can easily cause it to become unusable or even unworkable.
Semiconductors and Tube Preparation
The semiconductor industry encompasses the design, manufacturing and marketing of semiconductors. Semiconductors play an important role in the industry, particularly in the field of electronics.
Tube manufacturers and welders in the semiconductor industry have to cut the tubes before they can weld them. Today, we notice that the tube cutter is making its way into the industry. Tube cutting involves deburring and straightening the tube and sometimes repeating these steps several times: a process that can take several minutes.
Cutting the Tube Before Welding
When cutting a tube, it is essential to consider the end use and the expected result. If you just want to cut a tube, for example for a standard application, it is not always necessary to cut it orbitally.
Many different ways of cutting a tube are available on the market today. Whether you use manual cutting methods – such as a disc cutter or a hacksaw – or whether you use a band saw or a tube cutter, the result will not be ideal.
The first option, even with good dexterity on the part of the operator, will heat up the cut area, which will affect the tube thermally and denature it. The latter method may result in the tube being crushed, the cut not being perpendicular and maybe even a large burr on the inside of the tube.
Orbital cutting, on the other hand, will produce the cleanest result since the cut is carried out cold. The cold cut avoids the thermal impact, that could be caused by the cutting machine.
Furthermore, the AXXAIR orbital cutting machines are all equipped with stainless steel jaws and concentric clamping, which prevents pollution and deformation during clamping. This cannot be achieved with a band saw, tube cutter or circular saw.
If the intention is to subject the welds to strict controls, an orbital cut is the most suitable, since it provides perfect cutting geometry with nearly no defects.
Either way, an orbital cut will make the welder's job much easier, since there will not be any gap between the tubes to be connected. The tube will be ready for welding immediately after cutting, which constitutes a considerable time saving.
What is the Point of Tube Squaring?
Whether or not the tube has been cut orbitally, it can be squared afterwards. If the cut was made by hand, the squaring step will eliminate the cutting defects. If the cut is intended for strict markets and applications, squaring will smoothen the appearance of the tube to eliminate impurities and any variations in geometry.
The perpendicularity of the orbital cut is less than 0.25 mm, which means less material is lost. By choosing to cut with an orbital cutter, you are choosing a high precision cut.
What is the Advantage of Orbital Cutting in High Purity Industries?
Some of the "high purity" industries have zero tolerance for any welding defects: pharmaceutical, food & beverage, microchemical, semiconductor manufacturing or any other industry where a high level of welding quality is required and no element may interfere.
The application in which welding defects cost you the most is probably micro-fittings used in semiconductor manufacturing, pharmaceuticals, microchemicals and other industries where fluids pass through tubes less than 3 mm thick. Every single welding defect or improper handling, that renders a component unusable, constitutes a significant loss of money.
So this is where our CC81M cutting machine comes into play!
First off, the CC81M covers diameters from Ø5 mm (0.25") to Ø78 mm (3ʺ), which represents typically 95% of all tubes in the semiconductor industry. This industry commonly uses a tube cutter. However, this method requires a deburring and squaring of the tube, and in some cases these steps need to be repeated several times. This process can cost the operator several minutes.
The CC81M produces a high quality, burr-free cut with more or less .010" of perpendicularity. As a result, there is little or no need to invest further work into the tube. Not having to square the tube in a separate step also results in less wear and tear on the inserts, all while saving money on consumables and tubes.
Needless to say, the cut must be perfectly perpendicular, without any chips or dust. Otherwise, tube squaring is inevitable since no other method could guarantee such a clean cut.
The distance between the blade and the jaw is optimized to avoid vibrations and defects. This also increases the lifespan of the cutting blades. When an operator needs to cut very thin tubes with very small diameters (12 mm and less), the AXXAIR CC81M cutting machine is the ideal match since it features advantages that no other cutting machine can offer.
Using an AXXAIR cutting machine will save your business valuable time while guaranteeing the highest level of quality.
Which Additional Assets does the CC81M Offer?
The AXXAIR CC81M is the smallest machine in our orbital cutting range. However, if its 15 kilograms and compact dimensions are not enough to convince you, it has even more benefits in store for you. Underneath the skin of one of the smallest cutting machines on the market lies a high level of cutting precision and efficiency.
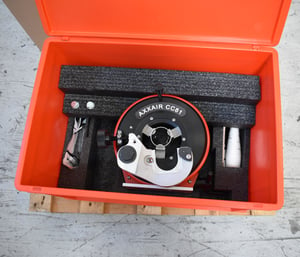
Its light weight makes transport easy and convenient, so it is ideal for on-site jobs. The motor and tools are packaged individually and delivered in a single transport case, protecting them from possible shocks and damage during transport.
Just like the other AXXAIR machines of the series, the CC81M is equipped with an anti-kickback system for the blade upon tube penetration.
The video below highlights our AXXAIR CC81M machine: discover the easy handling of its cutting system!
The electric swivel joint allows the machine to be used continuously, as it rotates without tethering the cord.
The concentric clamping system accounts for any ovality of the tube by bringing the clamping rod closer to the tube using 3 points or jaws. The CC81M is affordable and the cost can be quickly amortized by the production teams, making it a very moderate investment for your business.
The CC81M offers advantages that no other cutting machine on the market can match. It cuts small diameter tubes with precision, speed and quality. It is therefore suitable for all thin tube applications, ranging from standard applications to the most demanding requirements in all types of industries.
Download our product catalog to discover our full assortment of orbital cutting machines