The tungsten electrode plays a key role in the orbital TIG welding process since its use allows the electric arc to be obtained and its geometry directly influences the quality of the weld. Several criteria must be taken into account when choosing the electrode: material, diameter, length, size, geometry and surface condition of the electrode are parameters to be considered.
Among these criteria, we are focusing this article particularly on the diameter and geometry of the electrode.
How will the choice of the electrode diameter and geometry influence the electron flow behavior and thus the final weld in the TIG welding process? What is a flat spot and how to choose a suitable flat tip?
In this article we give you all the answers to these questions.
The role of a sharpened electrode in the welding process
Sharpening the electrode constitutes the most crucial parameter that influences the characteristics of the welding arc and the geometry of the weld bead. A sharpened electrode facilitates the arc initiation, but it can deteriorate rapidly, causing potential tungsten inclusions in the weld.
Sharpening must therefore be an integral part of the welding procedure. In order to guarantee optimal arc stability, sharpening must always be carried out in the longitudinal direction of the electrode. Perpendicular grinding must be avoided at all cost, as it will lead to arc instability and an entirely random welding result.
If the tip of the electrode is sharpened, there is a risk that the tip will become blunt and that tungsten will be released and drop into the weld bath, which would constitute a pollution of the weld.
This could then be visible as a white spot on an X-ray of the weld.
The importance of the flat spot
A flat tip helps to extend the life of the electrode but should be done carefully and not too large so as not to make the arc unstable and unchanneled. Making use of an adapted flat tip is therefore recommended to obtain arc stability, good electron transfer as well as an extended electrode life, without risking tungsten inclusions.
This figure illustrates the electron flow behavior as a function of the electrode geometry.
As shown here, the electrons always leave the electrode perpendicular to its surface.
It is important to opt for a flat tip at the end of the electrode, determined according to the current used. The use of an adapted flat tip will make it possible to create a linear output flow of electrons which we will call the effective flow.
This flow reaches the electrode in a very small area which will be the zone of maximum heating and will constitute the melting zone.
The more the flow is concentrated and the better the heat is focused on a confined zone, the more optimal the fusion will be. It is this action that will allow you – without needing the welder to execute a pendulum movement – to fuse up to 3 mm thickness in automatic.
The electron flow behavior as a function of the electrode diameter
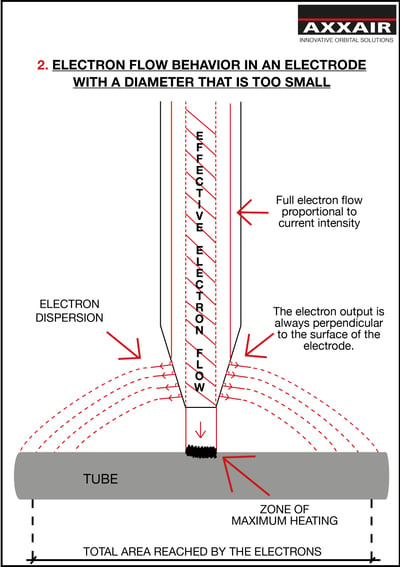
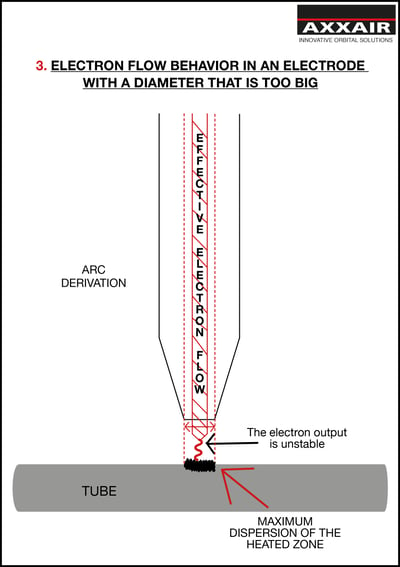
The figures above illustrate the influence of the diameter on the electron flow.
It can be observed that the choice of the electrode diameter is a determining factor since the electron flow within the electrode has a radius proportional to the intensity: the more amperes there are, the greater the flow will be. Let's imagine the case where the diameter of the flow is equivalent to the diameter of the flat spot (shown here in figure 1), then the effective flow is optimal when exiting the electrode.
On the other hand, in the case where the flow is larger than the flat tip (represented here in diagram 2), there will be a dispersion of the electrons which diffuse perpendicularly. The heating zone will then be wider and will lose its efficiency.
In the opposite case, where the flow would be smaller than the flat tip (shown here in figure 3), there is a risk of drift and instability of the arc because the effective flow cannot be channeled and "balances" on the flat tip: the heating zone is therefore spread out.
Since the electrons are not channeled at the exit, they will tend to gather in the corners and go sideways over the time of the low current (especially in the case of a weld that would require preparation with a bevel).
We therefore recommend choosing a suitable diameter and geometry in order to obtain arc stability, good electron transfer and thus ensure a long service life of the electrode without risking tungsten inclusions.
Would you like to know more about electrodes and how to choose the right electrode for orbital TIG welding?
Download our full guide here: